In modern metalworking and CNC precision manufacturing, twist drill bits are among the most commonly used drilling tools. Of all the available materials, HSS twist drills and carbide twist drill bits have become the most frequent choices for engineers. Buyers and users alike often ask: Which twist drill is better suited for my machining needs? Is investing in carbide twist drill bits worth it? Are HSS bits more economical and practical?
This article starts with the structural principles of twist drills and systematically analyzes the differences between HSS and carbide materials in terms of cutting efficiency, wear resistance, lifespan, cost, and applicable materials. Our goal is to help you understand how different twist drill types perform in real-world machining, especially when dealing with high-hardness materials like stainless steel, alloy steel, titanium alloy, or hardened tool steel.
Whether you’re aiming for a precision twist drill or seeking the most cost-effective drilling solution, this guide provides a comprehensive reference. By comparing the performance of HSS and carbide twist drills across high-speed machining, tool life, and cost control, we aim to help you make smarter, more efficient selection decisions.
What Is a Twist Drill Bit?
A twist drill bit is the most common drilling tool in industrial machining, mold manufacturing, and routine mechanical drilling. It gets its name from its distinctive helical flute design and is prized for its cutting performance, chip evacuation ability, and centering capability. Whether on traditional lathes, handheld drills, or high-speed CNC machines, twist drills are used across a wide range of materials including metals, plastics, and composites.
Basic Structure and Working Principle of Twist Drill Bit
A typical twist drill bit consists of:
- Cutting edge: At the tip of the bit, responsible for material removal.
- Helical flute: Designed for chip evacuation to prevent clogging.
- Point angle: Usually 118° or 135°, affects centering and cutting performance.
- Shank: Straight or tapered, used to mount the drill in the chuck or tool holder.
The drill operates by rotating and feeding axially into the workpiece. The cutting edge breaks the surface material, and through high-speed rotation and downward force, continuous drilling is achieved. Good geometric design enhances chip evacuation, reduces heat buildup, and extends tool life.
Main Functions and Application Scenarios of Twist Drill Bits
Twist drills are primarily used to create holes in solid materials. They’re suitable for operations such as through holes, blind holes, and pilot holes. Common use cases include:
- Pre-drilling for screw holes or dowel pins in mold making.
- Rapid drilling of metal structural parts and automotive components.
- High-precision, small-diameter holes in aerospace and medical applications (often using precision twist drills).
Different materials suit different tasks:
- HSS twist drills: Best for softer materials like aluminum, mild steel.
- Carbide twist drills: Ideal for hard-to-machine materials like stainless steel, hardened steel, and titanium.
Brief Comparison of Common Drill Types: HSS vs. Carbide
Twist drills typically fall into two categories:
- HSS twist drill bits: Offer excellent toughness and impact resistance. Suitable for medium-to-low speed cutting and are cost-effective. Widely used on steel, non-ferrous metals, and plastics.
- Carbide twist drill bits: Made of tungsten carbide, these have high hardness and heat resistance. Perfect for high-speed, high-feed machining of hard materials like stainless steel, titanium alloys, and hardened tool steels.
Precision twist drill bits are also available for applications requiring tight tolerances and fine surface finishes. These are used extensively in aerospace, medical, and high-end mold industries.
Introduction to HSS Twist Drill Bits: Economical and Practical All-Rounder
HSS twist drills are popular in metal fabrication, mechanical maintenance, and small-to-medium batch production due to their toughness, versatility, and low cost. For CNC users who need balanced performance and economy, HSS is a solid choice.
Features and Advantages of HSS
- High toughness: Less prone to breakage, ideal for interrupted cuts and handheld drills.
- Moderate heat resistance: Handles mid-range temperatures, suitable for low-to-medium speed drilling.
- Regrindable: Can be resharpened multiple times, lowering maintenance costs.
- Wide adaptability: Handles most softer metals, plastics, and wood.
Suitable Materials and Machining Conditions
HSS twist drills work well with:
- Low carbon steel, aluminum, copper.
- Plastics, nylon, wood.
- Low-speed or handheld drilling environments.
They can be used in general-purpose machines like drill presses, tailstock lathes, and basic milling machines. However, they’re not ideal for prolonged machining of hard metals due to wear from heat accumulation.
HSS Drill Bit Life, Cost-Effectiveness, and Limitations
HSS twist drills have a lower initial cost but also a shorter lifespan compared to carbide. Key pros and cons:
Advantages:
- Affordable for low-volume or custom jobs.
- Easily resharpened for reuse.
- Good for general-purpose drilling.
Limitations:
- Poor wear resistance in hard metals.
- Not suitable for high-speed, high-volume CNC operations.
- May lack precision and finish quality in demanding applications.
Carbide Twist Drill Bits: Built for High-Hardness Materials
As materials become harder, traditional HSS drills struggle to meet the demands of modern manufacturing. Carbide twist drills are the go-to solution for CNC users working with stainless steel, titanium alloys, and hardened tool steels, offering superior hardness, wear resistance, and heat tolerance.
Carbide Material Overview and Performance Benefits
Carbide, often tungsten carbide, is a composite of carbide particles and metal binders (typically cobalt), sintered at high temperatures. Key benefits:
- Extreme hardness: Maintains cutting ability even above 700°C.
- Superior wear resistance: Great for continuous drilling with minimal tool changes.
- High rigidity: Maintains dimensional accuracy under high-speed operation.
- Advanced geometries: Enables fine-tuned performance and surface finish.
Carbide twist drills excel in high-speed, high-precision CNC environments.
Best-Suited Materials for Carbide Drill Bits
Carbide bits are ideal for machining:
- Hardened tool steel (e.g. SKD61, S136 with HRC55-65)
- Stainless steel (e.g. 304, 316)
- Titanium alloys (e.g. TC4)
- Nickel-based alloys and high-strength cast irons
These materials require drills that resist heat and wear while maintaining sharpness and chip evacuation under stress.
High-Speed Cutting and Dry Machining Performance
Carbide drills perform best in:
- High-speed applications (>12,000 rpm)
- Dry or minimal-lubrication environments (MQL)
- Automated CNC setups in automotive, aerospace, medical industries
Coatings like TiAlN, DLC, and CVD diamond further enhance heat and wear resistance.
When Should You Use a Precision Twist Drill?
Precision twist drills are specialized tools designed for micron-level accuracy and surface quality. Compared to general-purpose drills, these feature tighter tolerances, premium carbide materials, and advanced coatings, making them ideal for high-end production.
CNC Applications Requiring Tight Tolerance Control
Precision twist drills are essential in mold making, high-precision mechanical parts, and automation systems. Tolerances are often held within ±0.01 mm. Applications include:
- Pilot holes for precision dowel pins.
- Guide holes for bearing assemblies.
- Any task requiring repeatable, concentric holes.
Internal coolant channels and low runout shank designs allow consistent results during long drilling cycles.
Aerospace, Medical, and Mold Industry Use Cases
Precision drills are used in:
- Aerospace: Titanium and superalloy components.
- Medical: Stainless steel implants and orthopedic drilling.
- Mold making: Complex cavity drilling with strict tolerances.
Their ability to avoid burrs, maintain straightness, and resist thermal distortion makes them irreplaceable in these sectors.
How to Identify and Select Precision Twist Drills
Key buying considerations include:
- Tolerance grade: Choose h6 or h7 depending on hole spec.
- Material and coating: Premium carbide with TiAlN, DLC, or diamond coating for wear resistance.
- Shank and runout precision: Lower runout means higher stability.
- Internal coolant: Essential for deep hole or heat-sensitive material drilling.
- Certifications and brand reputation: Prefer ISO/DIN-certified brands like Precision Twist Drill®, OSG, Kennametal, or Samho Tool.
白底-主图2-300x300.jpg)
Comparison: Carbide vs. HSS Twist Drill Bits – Which One Should You Use?
In modern metalworking and CNC precision manufacturing, the right twist drill bit significantly impacts production efficiency, part quality, and overall cost. Carbide twist drill bits and HSS twist drills dominate the market, each boasting strengths and trade-offs. This article offers a systematic side-by-side comparison—covering cutting efficiency, tool life, cost-effectiveness, and CNC usage recommendations—to support engineers in making informed choices.
Cutting Efficiency & Speed Capabilities
-
Carbide twist drills maintain high hardness—even at elevated temperatures due to “red hardness”—enabling stable performance at spindle speeds exceeding 12,000 RPM, which drastically boosts throughput.
-
In contrast, HSS twist drills are better suited to mid-to-low RPM ranges (typically under 6,000 RPM). Higher speeds result in heat buildup and premature wear.
-
Carbide excels in continuous, high-speed drilling operations for mass production. Meanwhile, HSS is ideal for intermittent drilling or low-volume, low-speed jobs.
Tool Life & Wear Resistance
-
Carbide bits outshine HSS in wear resistance, especially under the demands of hard metals like stainless steel, hardened tool steels, or titanium alloys. They sustain sharp cutting edges longer and keep wear rates low even when drilling at elevated temperatures.
-
HSS bits, while tough and resistant to shock loads, wear faster in abrasive or heat-intensive environments. Overuse often triggers edge chipping or thermal damage—compromising cut quality.
Cost-to-Performance
-
Upfront cost: HSS bits are cheaper—making them an economical choice for small shops and maintenance work.
-
Total cost: Carbide’s longer life and higher productivity often result in lower overall cost-per-hole, especially for high-volume production or tough materials.
-
ROI analysis: Consider factors like tool longevity, machine downtime, and regrind costs—carbide often delivers better returns in demanding scenarios.
CNC Machining Center Recommendations
-
For high-hardness materials and continuous, high-speed operations, opt for carbide twist drill bits to maintain consistent hole quality and casing surface finish.
-
For jobs involving low-hardness materials, small batches, or frequent material changes, HSS remains effective and budget-friendly.
-
Combine proper coolant/lubrication, coated drills, and internal coolant features to extend bit life and maintain drilling consistency across both types.

How to Choose the Right Twist Drill for Your Setup
Selecting the correct drill bit depends on matching it to 1) the material being drilled, 2) your machine’s speed and rigidity, and 3) your cost-benefit goals.
Material-Driven Selection
-
Soft alloys (e.g., aluminum, mild steel): HSS is a strong choice for affordability and toughness.
-
Hard metals (e.g., stainless steel, titanium, hardened steels): Go with carbide twist drill bits, which deliver exceptional wear resistance and heat tolerance.
-
For plastics or composites, specialized coatings or geometry may be necessary to prevent material build-up and improve chip flow.
Matching Drill Bit to Equipment Strength
-
Rigid, high-RPM CNC spindles excel with carbide bits at high feeds and speeds.
-
Lower-RPM machines or manual drill presses should use HSS bits to avoid tool damage from machine vibration or limited rigidity.
-
For deep-hole drilling: internal-coolant or through-coolant carbide bits help maintain cutting temperature and surface finish.
Balancing Efficiency with Total Cost
-
Carbide bits cost more upfront but deliver higher efficiency and longer service life.
-
HSS bits are less expensive and can be rechipped multiple times, suiting small-scale or budget-conscious applications.
-
A phased strategy—using HSS for prep work and carbide for finishing—often delivers the best balance of cost control and performance.
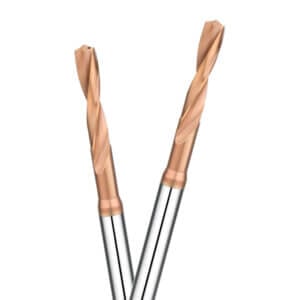
Choose Wisely Between HSS and Carbide
Understanding the strengths and limitations of each material is crucial for optimizing machining outcomes. HSS bits offer excellent toughness and cost-effectiveness in low-speed and soft-material contexts. In contrast, carbide twist drills provide unmatched durability, heat resistance, and production efficiency—justifying their higher price in demanding applications.
Summary of Pros and Cons
Feature | HSS Twist Drill | Carbide Twist Drill |
---|---|---|
Upfront Cost | Low | High |
Speed Compatibility | Mid-to-low RPM | High RPM |
Tool Life | Moderate | Long |
Impact Resistance | Strong | Lower |
Suitable Materials | Softer metals, plastics | Hard metals, alloys, CNC high-speed work |
Typical Use Case | Maintenance, small runs | Mass production, precise drilling |
Optimal Use Strategies
-
Roughing & low-cost runs: HSS is practical and efficient.
-
Finishing & harder materials: Switch to carbide for improved finish, accuracy, and lifecycle.
-
Challenging conditions: Use coated, internal-coolant carbide drills for deep-hole or dry/high-speed drilling.
By understanding your workpiece material, machine capabilities, and production scale, you can effectively leverage both HSS and carbide twist drill technologies for best performance and cost control.
FAQ
What is a twist drill bit?
A twist drill is a spiral-grooved cutting tool used in metallurgical and mechanical operations. It uses rotation and axial feed to create holes in materials like steel, aluminum, stainless steel, and plastic.
Can HSS twist drills drill stainless steel?
Yes—within limits. HSS (or cobalt-enhanced HSS, like M35/M42) can handle light-duty stainless steel drilling under controlled speeds and adequate cooling. For heavy-duty or long runs, carbide bits are strongly recommended.
How do carbide and cobalt alloy twist drills differ?
-
Carbide drills (tungsten-carbide bonded) offer high hardness and wear resistance—ideal for hard metals and high-speed work.
-
Cobalt-alloy HSS drills contain cobalt for better heat resistance than standard HSS, offering a middle ground in cost and performance.
When should you use a precision twist drill?
Ideally suited for tasks demanding sub-0.01 mm tolerances, perfect concentricity, and superior surface finish—such as aerospace, medical, or mold drilling. Pair with rigid tooling and internal cooling to unlock full capability.