
In the field of end mill processing of copper metal, the processing technology of various copper materials is the tireless pursuit of CNC engineers. Achieving efficient copper machining depends on a deep understanding of both material properties and complex tooling. Different copper alloy processing requires different methods, from selecting a more suitable end mill to fine-tuning the cutting parameters, it is very important. Crucially, factors such as material hardness, tool materials and cutting strategies all play an important role in improving machining efficiency and workpiece quality.
Addressing the complexity of copper machining requires a holistic strategy that encompasses end mill tool selection, cutting technology and process optimization. By delving into nuances such as end mill tool geometry and cutting forces, engineers can alleviate the stress encountered during machining and unlock the end mill’s full potential for machining copper. Through careful planning and continuous improvement initiatives, increasing efficiency in processing copper becomes not only a goal, but an achievable reality.
Analysis of Copper Material Hardness
In the metal processing industry, understanding the hardness differences between different copper materials is very important for efficient processing of copper materials. Copper and its alloys have different HRC hardnesses, which affects end mill tool selection and machining strategies differently. Pure copper, brass, bronze, tungsten copper, copper-nickel alloy and copper-aluminum alloy all have different effects in processing.
Hardness Variations Among Copper Materials
- Pure Copper: Known for its excellent thermal and electrical conductivity, pure copper has a relatively low hardness. This makes it easier to machine but prone to generating burrs and requiring more precise tool control.
- Brass: A copper-zinc alloy, brass offers improved hardness over pure copper, enhancing its machinability. It is commonly used in applications requiring a good balance of strength and workability.
- Bronze: This alloy of copper and tin (and sometimes other elements) is harder than brass and pure copper. Its increased hardness provides better wear resistance, making it suitable for high-stress applications.
- Tungsten Copper: Combining the properties of tungsten and copper, this alloy exhibits high hardness and excellent thermal resistance. It is particularly challenging to machine and demands robust, wear-resistant tools.https://samhotool.com/tungsten-end-mill/
- Copper-Nickel Alloys: These alloys, known for their corrosion resistance, have a hardness level that varies depending on the nickel content. Higher nickel content increases hardness and reduces machinability.
Copper-Aluminum Alloys: Featuring improved strength and hardness, these alloys are used in applications requiring high mechanical performance. They are more difficult to machine than pure copper and require specialized tooling.
Tool Selection Based on Hardness
When processing copper materials with different hardnesses, it is very important to choose the appropriate end mill. For machining softer materials like pure copper, high-speed steel (HSS) end mills are sufficient, offering excellent sharpness and cutting capabilities. For harder alloys such as bronze or tungsten copper, carbide end mills are very suitable. Because carbide end mills have unparalleled hardness and excellent wear resistance.
Tool geometry also plays an important role. End mills with larger rake angles are beneficial to processing softer materials and can effectively reduce cutting force and heat generation. On the contrary, for harder copper alloys, end mills with smaller rake angles and stronger edge strength are preferred to withstand higher cutting loads and avoid edge collapse.
Analyzing the hardness of copper materials can play a very good role in selecting the correct tool and continuously improving the machining process. Understanding the unique characteristics of pure copper, brass, bronze, tungsten-copper, copper-nickel alloys and copper-aluminum alloys is of great help to CNC engineers to customize corresponding methods to ensure efficient and precise machining of different copper materials. It is crucial to achieve the target requirements for copper machining by selecting tools based on the hardness of the copper material.

Preheating Treatment
Preheat treatment can be of great help in the cutting of certain copper alloys. By heating before processing, the cutting performance of the material can be enhanced and the processing difficulty and related costs can be reduced. This treatment is particularly beneficial for alloys such as pure copper, brass, bronze, tungsten copper, copper-nickel alloy, copper-aluminum alloy, etc.
Benefits of Preheating for Different Copper Alloys
- Pure Copper: Preheating pure copper can reduce its inherent stickiness and improve its machinability. Elevated temperatures help in softening the material slightly, making it easier to cut and reducing tool wear.
- Brass: For brass, preheating can help in relieving internal stresses and reducing brittleness. This results in smoother cuts and less tool chatter, improving overall machining efficiency and surface finish.
- Bronze: Preheating bronze, which is harder than pure copper and brass, can soften the alloy, making it easier to machine. This process helps in reducing tool wear and extending tool life, particularly during high-speed operations.
- Tungsten Copper: Tungsten copper, known for its high hardness and thermal conductivity, benefits greatly from preheating. The process reduces the brittleness of tungsten copper, making it more ductile and easier to machine without causing excessive tool wear.
- Copper-Nickel Alloys: These alloys can become work-hardened quickly. Preheating helps in reducing this tendency, allowing for smoother cuts and reducing the frequency of tool changes. It also aids in maintaining a consistent material structure during machining.
- Copper-Aluminum Alloys: Preheating copper-aluminum alloys can reduce their hardness and improve ductility, making them easier to machine. This process helps in achieving better surface finishes and extending tool life.
Practical Considerations and Techniques
Implementing a preheat treatment requires careful control of temperature and heating duration to avoid overheating, which can adversely affect material properties. Typically, copper alloys are preheated to temperatures ranging from 150°C to 300°C, depending on the specific alloy and its composition.
During copper alloy preheating, uniform heating is critical as it prevents warping and residual stresses caused by thermal gradients. For even heating, it is recommended to use a convection oven or induction heater, both of which provide controlled and consistent heating. In addition, precision instruments should be used to monitor the material temperature to ensure it reaches the optimal preheating temperature to maximize processability.
In addition to even heating, the copper alloy must be held at the preheat temperature for a sufficient period of time to ensure even heat distribution within the material. This step is critical to realizing the full benefits of preheat treatment, including reduced tool wear and improved cutting performance.
Preheat treatment is a key technology to improve the cutting performance of various copper alloys, including bronze, tungsten copper, copper-nickel alloys and copper-aluminum alloys. By carefully heating materials before machining, CNC engineers can significantly improve the material’s processing properties and gain the following benefits.
- Reduce material hardness: Heating softens the material, making it easier to process, reducing tool cutting resistance and reducing tool wear.
- Improved material ductility: Preheated materials are more ductile and less likely to break, thereby improving processing safety and reducing scrap rates.
- Improve the quality of machined surfaces: Good machinability helps to obtain smoother and finer machined surfaces, improving the overall quality of parts.
- Simplify the processing process: Preheating can reduce the difficulty of processing, make the processing process smoother, and reduce processing time and costs.

Selection of Tool Materials
When processing copper materials with different hardnesses, the choice of end mill tool material is very important for processing efficiency and life. Different copper alloys, such as bronze, tungsten copper, copper-nickel alloy, copper-aluminum alloy, etc., require specific tool materials to achieve efficient and precise machining. For harder copper materials, tools with high wear resistance and thermal stability must be selected, such as carbide or wear-resistant coated tools.
Tool Material Choices for Different Copper Hardness Levels
- Pure Copper: Pure copper, with its relatively low hardness, can be effectively machined using high-speed steel (HSS) tools. However, for higher efficiency and longer tool life, carbide tools are recommended. These tools offer better wear resistance and can handle higher cutting speeds.
- Brass: Brass, being harder than pure copper, benefits from using carbide tools. Carbide tools maintain sharp cutting edges longer and reduce tool change frequency, enhancing productivity.
- Bronze: The increased hardness of bronze necessitates the use of even more durable tools. Carbide tools are ideal, but coated carbide tools, such as those with titanium nitride (TiN) or aluminum titanium nitride (AlTiN) coatings, provide additional wear resistance and thermal protection.
- Tungsten Copper: Tungsten copper is particularly challenging due to its high hardness and thermal conductivity. Tools made from solid carbide or coated carbide are essential. Coatings like diamond or cubic boron nitride (CBN) can further improve tool performance by offering superior hardness and thermal resistance.
- Copper-Nickel Alloys: These alloys, especially those with higher nickel content, require robust tooling. Carbide tools with TiN or TiAlN coatings are effective in managing the increased hardness and maintaining cutting efficiency.
- Copper-Aluminum Alloys: Copper-aluminum alloys, known for their strength, demand high-performance tools. Carbide tools with specialized coatings, such as AlTiN or diamond-like carbon (DLC), provide the necessary hardness and thermal stability to machine these materials efficiently.
Benefits of Coated Tools
There are several advantages to using coated tools when machining harder copper materials. The layer can effectively reduce the friction between the tool and the workpiece, thereby reducing cutting resistance, reducing heat, and reducing tool wear. Coated tools have higher hardness and wear resistance, can withstand more severe processing conditions, and extend tool life. For example, TiN and TiAlN coatings are ideal for general-purpose machining, while diamond and DLC coatings provide superior performance for the most demanding applications. These coatings enable higher cutting speeds and feeds, resulting in increased productivity and better surface finishes.
Choosing the right end mill tool material is critical to effectively machining copper materials of varying hardness. For pure copper, high speed steel and carbide tools are effective, while harder alloys such as bronze and tungsten copper require more robust solutions such as coated carbide tools. Coatings such as TiN, AlTiN, diamond and DLC improve tool performance and ensure their wear resistance and thermal stability. By selecting the appropriate end mill tool material based on copper alloy hardness, CNC engineers can optimize the machining process to achieve superior efficiency, accuracy and machining quality. Coated carbide cutting tools are the best choice for machining hard copper alloys, which can significantly improve tool performance and processing results.

Rational Selection of Tool Diameter
Choosing the right tool diameter is critical for machining copper materials of varying hardness. Choosing the correct diameter improves machining efficiency and tool life, resulting in production cost savings. This is suitable for processing pure copper, brass, bronze, tungsten copper, copper-nickel alloy, copper-aluminum alloy and other materials to achieve high efficiency, high precision and high quality processing results.
Importance of Tool Diameter in Machining
- Pure Copper: Pure copper is relatively soft and ductile. Using a smaller diameter tool can provide greater precision and finer cuts, but it may wear out quickly due to the material’s tendency to adhere to the tool. A slightly larger diameter tool can help distribute cutting forces more evenly, improving tool life and reducing the risk of tool breakage.
- Brass: Brass, being harder than pure copper, allows for the use of smaller diameter tools without excessive wear. However, using a tool with too small a diameter can lead to higher cutting forces and potential tool deflection. A balanced diameter helps maintain accuracy and extends tool life.
- Bronze: The increased hardness of bronze necessitates a careful selection of tool diameter. A larger diameter tool is preferred to handle the higher cutting forces and reduce wear. This choice also helps in maintaining rigidity and preventing tool deflection during machining.
- Tungsten Copper: Tungsten copper’s high hardness and brittleness require robust tools. A larger diameter tool is essential to distribute the significant cutting forces encountered. This approach minimizes tool wear and enhances the overall stability of the machining process.
- Copper-Nickel Alloys: These alloys can be tough to machine due to their work-hardening properties. A larger diameter tool can help manage the cutting forces and reduce tool wear. It also aids in achieving better surface finishes and maintaining dimensional accuracy.
- Copper-Aluminum Alloys: These alloys, known for their strength, benefit from a larger diameter tool to handle the higher cutting forces. This selection helps in achieving efficient material removal rates while maintaining tool longevity and machining precision.
Practical Guidelines for Selecting Tool Diameter
Selecting the right tool diameter involves considering several factors, including material hardness, cutting forces, desired surface finish, and tool stability. Here are some practical guidelines.
- Tool Rigidity: Larger diameter tools provide greater rigidity, which is crucial for machining harder copper alloys. This rigidity helps in maintaining accuracy and preventing tool deflection.
- Cutting Force Distribution: A larger tool diameter distributes cutting forces over a wider area, reducing the stress on any single point of the tool. This distribution is beneficial for harder materials, where concentrated forces can lead to rapid tool wear or failure.
- Surface Finish Requirements: For applications requiring fine surface finishes, smaller diameter tools can provide higher precision and finer cuts. However, tool wear must be monitored closely to maintain quality.
- Machining Efficiency: Balancing tool diameter with machining efficiency is key. Larger tools can remove more material per pass, improving productivity, while smaller tools might be necessary for intricate details or tight tolerances.
When machining copper alloys, choosing the right tool diameter is crucial. It can affect machining efficiency, tool life, machining accuracy and surface quality. Generally speaking, the larger the tool diameter, the faster the cutting speed, but the greater the cutting force. For harder copper alloys, a smaller tool diameter should be selected to reduce cutting forces and improve machining accuracy. For softer copper alloys, larger tool diameters can be selected to increase cutting speed and processing efficiency. By properly selecting the tool diameter, CNC engineers can optimize the machining process and achieve efficient, high-precision and high-quality copper alloy processing.
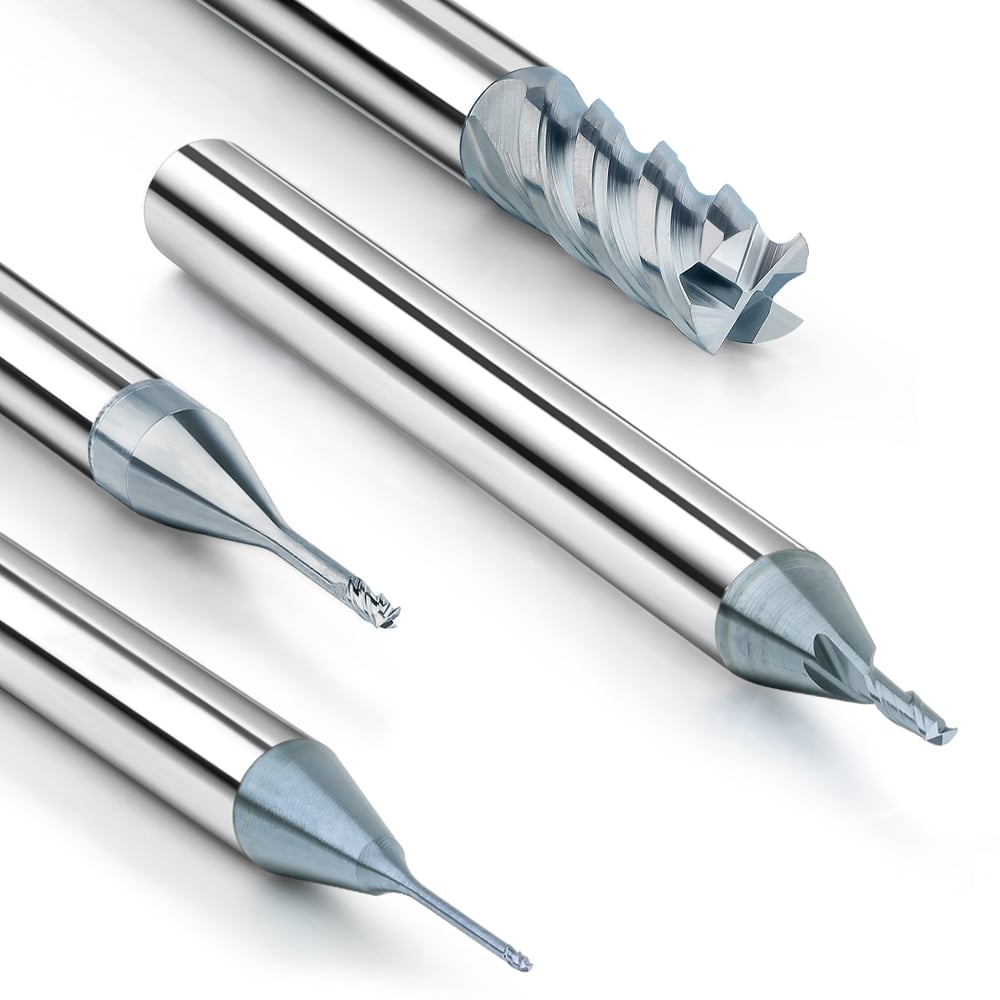
Optimization of Tool Geometry
For copper alloys of varying hardness, including pure copper, brass, bronze, tungsten copper, copper-nickel alloys, and copper-aluminum alloys, choosing the right tool geometry is critical. Tool geometry, including factors such as tool tip angle, number of grooves, and edge design, will directly affect cutting efficiency and surface quality.
Key Elements of Tool Geometry
- Tool Tip Angle: The tool tip angle affects the cutting force and heat generation. For softer materials like pure copper, a larger tip angle can reduce the risk of material adhesion and improve surface finish. Harder materials like tungsten copper require a smaller tip angle to enhance tool strength and reduce the risk of chipping.
- Number of Flutes: The number of flutes impacts chip evacuation and cutting stability. For pure copper and brass, tools with fewer flutes (e.g., two or three) are ideal as they provide better chip clearance and reduce clogging. For harder materials like bronze and tungsten copper, tools with more flutes (e.g., four or more) offer better stability and distribute cutting forces more evenly.
- Edge Design: The edge design, including rake angle and relief angle, plays a vital role in cutting performance. For pure copper and softer alloys, a sharp edge with a positive rake angle reduces cutting forces and enhances surface finish. For harder materials, a rounded edge with a negative or neutral rake angle increases tool strength and durability.
Tailoring Tool Geometry for Specific Copper Alloys
- Pure Copper: For pure copper, which is soft and ductile, tools with a larger tip angle (e.g., 60 degrees), two or three flutes, and a sharp edge with a positive rake angle are optimal. This geometry minimizes material adhesion and ensures a smooth finish.
- Brass: Brass, being slightly harder than pure copper, benefits from a similar tool geometry. A tip angle of around 60-70 degrees, two to four flutes, and a sharp edge with a positive rake angle help achieve efficient cutting and good surface quality.
- Bronze: Bronze requires a more robust tool geometry due to its increased hardness. A smaller tip angle (e.g., 50 degrees), four or more flutes, and a rounded edge with a neutral rake angle provide the necessary strength and stability for efficient machining.
- Tungsten Copper: Tungsten copper, with its high hardness, demands a very sturdy tool geometry. A tip angle of around 45-50 degrees, four or more flutes, and a negative rake angle edge design are essential to withstand the high cutting forces and prevent tool wear.
- Copper-Nickel Alloys: These alloys, which can vary in hardness, typically require a moderate tip angle (e.g., 55-60 degrees), three to four flutes, and a neutral rake angle edge. This combination balances cutting efficiency and tool life.
- Copper-Aluminum Alloys: Copper-aluminum alloys, known for their strength, benefit from a moderate tip angle (e.g., 55-60 degrees), four or more flutes, and a slightly positive rake angle edge. This geometry ensures good cutting performance and chip evacuation while maintaining tool durability.
The Importance of Tool Geometry in Copper Alloy Machining
Tool geometry is one of the key factors affecting the processing efficiency and surface quality of copper alloys. By choosing the right tool geometry for copper alloys of varying hardness, CNC engineers can significantly improve machining performance and achieve optimal results.
For softer copper alloys such as pure copper and brass, the following tool geometries are recommended:
- Larger tool tip angle: helps improve cutting efficiency and reduce cutting forces.
- Fewer flutes: reduces friction with the workpiece and results in a smoother surface finish.
- Sharp edge design: Helps achieve sharper cutting edges and more precise processing.
For harder copper alloys such as bronze and tungsten copper, the following tool geometries are recommended:
- Smaller tip angle: Provides greater strength and smaller cutting deformation to withstand higher cutting forces.
- More flutes: effective chip removal, reducing heat build-up in the cutting area.Sturdy edge design: improves tool wear resistance and extends tool life.

Avoiding Vibration and Resonance
When processing soft copper materials such as pure copper, brass, bronze, tungsten copper, copper-nickel alloy, copper-aluminum alloy, it is important to prevent tool vibration and resonance. To reduce vibrations and deflections and ensure a stable machining process, suitable tool and workpiece securing measures are required.
Understanding the Impact of Vibration
- Tool Vibration: Excessive tool vibration can lead to poor surface finish, dimensional inaccuracies, and accelerated tool wear. It occurs when the cutting tool oscillates during machining due to insufficient rigidity or improper cutting conditions.
- Resonance: Resonance occurs when the natural frequency of the tool or workpiece matches the frequency of the cutting forces, leading to amplified vibrations. Resonance can cause catastrophic tool failure, surface finish issues, and reduced machining accuracy.
Strategies to Minimize Vibration and Resonance
- Optimizing Cutting Parameters: Adjusting cutting parameters such as cutting speed, feed rate, and depth of cut can help avoid resonance frequencies and minimize tool vibration. Optimal parameters ensure stable cutting conditions and reduce the risk of vibration-induced issues.
- Tool Selection: Choosing the appropriate tool material, geometry, and coating can enhance tool rigidity and dampen vibrations. Tools with higher stiffness and damping characteristics are less prone to vibration and resonance, ensuring smoother machining operations.
- Workpiece Fixation: Properly securing the workpiece on the machine bed or fixture prevents unwanted movement during machining. Using clamps, vises, or dedicated workholding devices ensures stable workpiece support and minimizes vibration-induced errors.
- Toolholder Rigidity: Selecting a rigid and stable toolholder is crucial for minimizing tool deflection and vibration. High-quality toolholders with precision collets or hydraulic chucks provide better tool support and reduce the likelihood of resonance.
- Damping Techniques: Implementing damping techniques such as adding vibration-dampening materials or using tuned mass dampers can absorb vibration energy and minimize resonance effects. Damping systems effectively reduce vibration amplitudes, enhancing machining stability.
- Machine Condition Monitoring: Regular maintenance and monitoring of machine tool condition help identify and address potential sources of vibration, such as worn bearings or loose components. Maintaining machine tool rigidity ensures stable machining performance and reduces the risk of vibration-related issues.
Importance of Machining Stability
When using soft copper materials, it is very important to ensure the stability of the processing process to obtain high-quality processing results. By employing strategies that minimize vibration and resonance, CNC engineers can increase machining efficiency, extend tool life, and maintain high dimensional accuracy in workpieces. A stable machining environment minimizes the risk of errors and increases overall productivity.
Avoiding tool vibration and resonance is a critical step for efficient machining of copper materials such as pure copper, brass, bronze, tungsten copper, cupro-nickel alloys and copper-aluminum alloys. By understanding the effects of vibration, and by taking appropriate precautions such as optimizing cutting parameters, selecting the right tool, effectively securing the workpiece, and maintaining machine tool rigidity, CNC engineers can ensure the stability of the machining process and thus achieve satisfactory machining results. Prioritizing the stability of the processing environment can effectively reduce risks caused by vibration, increase productivity and maintain processing accuracy.

Optimization of Cutting Parameters
For different types of copper alloys such as pure copper, brass, bronze, tungsten copper, copper-nickel alloy and copper-aluminum alloy, it is crucial to choose the appropriate cutting parameters, which directly affects the processing efficiency and final results. In order to achieve optimal machining performance, parameters such as cutting speed, feed rate and depth of cut must be adjusted according to the characteristics of the material.
Understanding Material Characteristics
- Pure Copper: Being relatively soft and ductile, pure copper requires moderate cutting parameters to prevent excessive tool wear and maintain good surface finish. Higher cutting speeds and feed rates can be employed, but care must be taken to avoid chip adhesion and built-up edge formation.
- Brass: Brass is slightly harder than pure copper, necessitating slightly higher cutting speeds and feed rates. However, the material’s tendency to work harden requires careful consideration of tool engagement to avoid premature tool wear and maintain dimensional accuracy.
- Bronze: With its increased hardness compared to pure copper and brass, bronze typically requires lower cutting speeds and feed rates. Controlling cutting forces through reduced depths of cut and moderate feed rates helps prevent tool wear and maintain surface finish.
- Tungsten Copper: Tungsten copper is highly abrasive and heat-resistant, requiring conservative cutting parameters. Lower cutting speeds and feed rates, combined with smaller depths of cut, are necessary to manage tool wear and heat generation effectively.
- Copper-Nickel Alloys: These alloys exhibit varying degrees of hardness depending on the nickel content. Moderate cutting parameters are generally suitable, with adjustments made based on specific alloy properties to achieve optimal machining performance.
- Copper-Aluminum Alloys: Copper-aluminum alloys are known for their strength and heat dissipation properties. Higher cutting speeds and feed rates can be applied, but care must be taken to avoid overheating and tool wear.
Strategies for Parameter Optimization
- Cutting Speed: Adjusting cutting speed based on material hardness and thermal conductivity is crucial. Higher cutting speeds can improve productivity, but excessive speeds may lead to overheating and tool wear. Finding the optimal balance ensures efficient material removal while maintaining tool life.
- Feed Rate: Feed rate influences chip formation, tool wear, and surface finish. Higher feed rates increase material removal rates but may result in poor surface quality or tool breakage. Fine-tuning feed rates based on material properties and tool capabilities optimizes machining efficiency.
- Depth of Cut: Controlling depth of cut is essential for managing cutting forces, tool deflection, and chip evacuation. Deeper cuts increase material removal rates but may lead to vibration or chatter. Adjusting depths of cut according to material hardness and machine rigidity ensures stable and efficient machining processes.
Importance of Parameter Optimization
Optimizing cutting parameters for copper alloys with different properties (such as pure copper, brass, bronze, tungsten copper, copper-nickel alloys and copper-aluminum alloys) is the key to achieving efficient and productive machining operations. By carefully adjusting parameters such as cutting speed, feed rate and depth of cut, CNC engineers can significantly improve machining efficiency and achieve optimal results. By taking a systematic approach to optimizing cutting parameters, CNC engineers can ensure consistency and stability in the machining process, maximize material removal rates, extend tool life and achieve high-quality surface finishes. This is critical for efficient, high-yield processing of copper alloys.

Cutting Lubrication and Cooling
For copper materials that generate a lot of heat during processing, such as pure copper, brass, bronze, tungsten copper, copper-nickel alloy, copper-aluminum alloy, etc., it is necessary to choose appropriate cutting lubricants and coolants. Proper lubrication and cooling can reduce tool wear, improve the quality of machined workpieces, and effectively prevent thermal damage to tools and workpieces.
Importance of Lubrication and Cooling
- Heat Dissipation: Copper materials tend to conduct heat away from the cutting zone, leading to significant thermal loads on the cutting tool. Effective lubrication and cooling help dissipate this heat, maintaining tool integrity and preventing thermal expansion of the workpiece.
- Tool Wear Reduction: High temperatures can accelerate tool wear, especially when machining harder copper alloys. Lubricants and coolants reduce friction at the cutting interface, extending tool life and maintaining cutting performance.
- Surface Quality: Proper cooling and lubrication improve surface finish by reducing built-up edge formation and preventing material adhesion to the cutting tool. This results in smoother surfaces and higher dimensional accuracy.
Types of Lubricants and Coolants
- Water-Soluble Coolants: These coolants are effective for most copper materials due to their excellent heat dissipation properties. They are commonly used in machining pure copper, brass, and copper-aluminum alloys. Their high cooling capacity reduces thermal damage and helps maintain tool sharpness.
- Oil-Based Lubricants: Oil-based lubricants provide superior lubrication but may have lower cooling efficiency compared to water-soluble coolants. They are suitable for materials like bronze and copper-nickel alloys, where lubrication is critical to prevent tool wear and achieve good surface finishes.
- Synthetic and Semi-Synthetic Fluids: These fluids offer a balance between cooling and lubrication. They are versatile and can be used for a variety of copper alloys, including tungsten copper, which requires both effective heat dissipation and lubrication to prevent rapid tool wear.
Application Techniques
- Flood Cooling: Flood cooling involves a continuous stream of coolant directed at the cutting zone. This method ensures maximum heat dissipation and lubrication, making it ideal for high-speed machining operations involving softer copper materials like pure copper and brass.
- Mist Lubrication: Mist lubrication uses a fine spray of lubricant mixed with air, providing effective cooling and lubrication with minimal fluid consumption. This technique is suitable for harder copper alloys like bronze and copper-nickel alloys, where excessive coolant flow might be unnecessary.
- High-Pressure Coolant Systems: High-pressure coolant systems deliver coolant at high pressures directly to the cutting zone. This method is particularly effective for hard and heat-resistant materials like tungsten copper, ensuring thorough cooling and chip evacuation.
Selecting the Right Coolant and Lubricant
- Material Compatibility: Choose coolants and lubricants that are compatible with the specific copper alloy being machined. For example, water-soluble coolants are suitable for pure copper and brass, while synthetic fluids may be better for tungsten copper.
- Machining Operation: The choice of coolant and lubricant should also depend on the machining operation. High-speed operations may require flood cooling, while precision operations might benefit from mist lubrication.
- Environmental and Safety Considerations: Consider the environmental impact and safety of the coolants and lubricants. Non-toxic, biodegradable options are preferred for minimizing environmental impact and ensuring workplace safety.
Choosing appropriate cutting lubrication and cooling methods is an important part of efficient copper processing for processing heat-prone copper materials. Through this measure, tool wear can be reduced, workpiece surface quality improved, and overall machining efficiency improved during copper machining. According to the characteristics of copper alloy and appropriate cutting lubrication and cooling methods, the best processing performance and cost-effectiveness can be achieved, thereby obtaining high-quality machined parts and effectively extending tool life.

Understanding the nuances of copper machining involves many aspects, including material properties, tool selection and machining techniques. For example, softer materials like pure copper and brass require careful consideration of tool geometry and lubrication methods to mitigate thermal damage and ensure a smooth cut. In contrast, machining of harder copper alloys such as bronze and tungsten copper requires strong tools and optimized cutting parameters to withstand higher cutting forces and maintain dimensional accuracy. In addition, minimizing vibration and resonance is important for a stable machining process, especially when working with soft copper materials that are prone to vibration and tool deflection. By considering these factors and implementing appropriate techniques, CNC engineers can unleash the full potential of copper machining, achieving high efficiency and satisfactory workpiece quality during production.
Overall, optimizing copper machining involves a thorough understanding of the material properties and meticulous attention to the details of tool selection and machining strategies. By customizing cutting parameters, selecting the right lubricants and coolants, and minimizing vibrations and resonances, CNC engineers can achieve efficiency gains and excellent workpiece quality in machining. Using different copper processing methods not only improves productivity, but also ensures tool life and the integrity of machined parts. As technology continues to be refined and adapted to evolving technologies, the pursuit of excellence in copper processing remains an ongoing effort, driving innovation and advancement in the metal processing industry.